
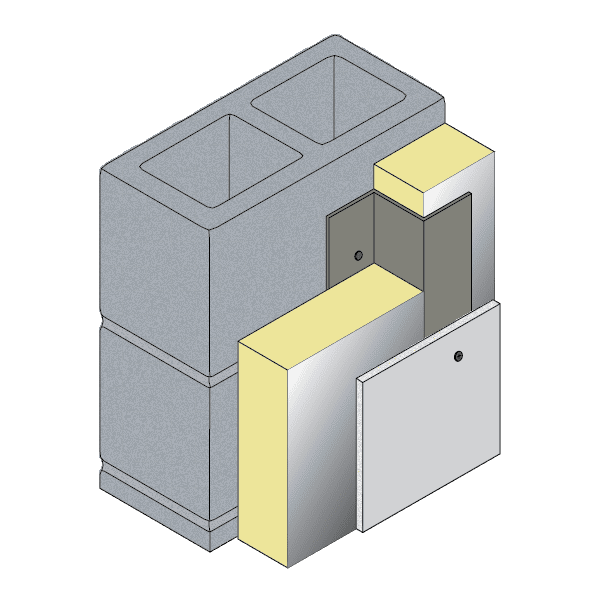
After visiting the Canfield Middle School worksite, we drove a few miles to downtown Coeur d’Alene to chat with Scott Fischer of Architects West. With over 40 years in business and projects spanning Idaho, Washington, Montana, and Oregon it was no surprise to see that the firm was filled with countless framed awards, articles and news clippings from various projects over the years.
Fischer’s decision to specify InSoFast panels for the Canfield project focused heavily on achieving extreme energy efficiency. To do so, Fischer sought an alternative to traditional systems like Z-furring which can lose much of their R-value to conductive thermal bridging.
InSoFast is also more cost effective: We requested a quote from a supplier local to Architect’s West in Oregon for a 1,000 sq-ft installation using Z-furring. The material costs alone came at about $100 more than the InSoFast UX 2.0 method specified by Architects West. See comparison below.
Architects West vision entails creating “a culture that fosters and promotes objective thinking in the process of providing comprehensive design solutions”. They also “encourage educating [their] team to keep pace with an ever-changing and complex world of technology and sustainability.” We settled into Fischer’s office to talk InSoFast, the Canfield Project, and their vision as architects.
Tell us a bit about your background as an architect. How long you have been working for Architects West Inc?
My name is Scott Fischer and I am one of the Managing Principals of Architects West. I’ve been with the firm for 31 years. We’re a full service design firm in Coeur d’Alene, Idaho with 28 employees and we’re strangely enough one of the bigger architectural firms in the state.
Our practice over the past 35 years has largely been school related projects- about 65% of what we’ve done historically has been K-12 projects. But we also work on a variety of projects from prisons to single family residences.
Doug Cossette of Spokane Wall Systems was originally the one that suggested using InSoFast UX 2.0 panels for the Canfield Middle School Project. What were the key factors that made you decide to specify InSoFast for the project?
Doug brought me the information on InSoFast about two years ago. We often have situations in school projects where we know we want to have a durable product. With the new energy codes we have to think about not only increasing the energy efficiency of the wall but also maintaining durability. So in gymnasiums, for instance, we often use concrete block products and then we have to figure out a way to insulate those walls.
When Doug introduced InSoFast we thought it would be a pretty natural way to get a continuous insulation barrier against a durable wall.
Energy codes have been changing a great deal over the past couple of years. We’re finding that there are some big issues with thermal short circuiting that happens through Z-channels. The metal Z-channels transfer a great deal of heat from one side of the wall to the other.
InSoFast panels are pretty much continuous other than the plastic ladder which gives you something to attach your substrate to on the inside. It’s a much better way to get an even and consistent thermal performance all the way across the wall surface.
Comparing 1,000 sq-ft:
Traditional: R-Value 5.6
UX 2.0: R-Value 8.5
EX 2.5: R-Value 10.5
At Canfield we had a little over 10,000 square feet of wall surface, with almost 7,000 square feet in the gym where we were looking to use MDO (medium density overlay) plywood. We’re using InSoFast for this space and so far we’re pretty excited to see it through fruition. So far only the classroom portion of the project has been installed, which will have gypsum drywall installed over the top of the InSoFast panels.
Did you have any initial reservations about specifying InSoFast for the Canfield Elementary addition?
In school projects we do a lot of concrete block and we knew we needed something that would be able to accommodate raceways for electrical systems. Typically in block construction we cut raceways into the block and the mason works with the electrician to install them anyway.
It’s probably more likely in a residential situation that you would use the channels that are routed directly into the InSoFast panel, so that aspect wasn’t really a sales feature for me. Like I said, the bigger thing for me was to get a layer of continuous insulation across that block surface so we could eliminate those short circuits.
After your experiences with InSoFast for the Canfield Middle School addition, would you consider using InSoFast for future projects?
Of course the project is still in the works, so there’s no way to tell at this point how the Canfield Middle School project will turn out, but I think using InSoFast will be a great alternative to what we have used in the past.
Another problem with using metal shaped Z-Furring is that after anywhere from 5-10 years you begin to see dark spots showing through the drywall and paint where the screws attach the drywall into that Z-Shaped fastener. This happens because the thermal moisture transitions from the cold surface to the warm surface. Since we’re attaching our screws into the plastic web that issue will go away.
We caught up with Scott Fischer to see how the project panned out. He said “The project turned out well; my only reservation was that in corners, the plastic “ladders” embedded within the insulation that allow the GWB (or, in the case of this gym, the MDO plywood) to be attached, do not occur until 8” away from the corner. Therefore GWB is unsupported in the corner and it is taped and ultimately may move and crack. Perhaps “starter” pieces should be developed to provide support for the subsequent GWB”
To address these concerns we’d like to point out that when InSoFast walls are solidly supported in this case by masonry sub-walls there will be very little chance for the drywall to move, flex or crack.
If an InSoFast wall is backed (glued on to masonry) and adjoins a framed wall (16” oc studs) then it would be important to fasten the drywall in the corner. That is simple enough to do by using a metal corner angle (3″ x 3″, 25ga sheet metal) adhered to the InSoFast. Our Drywall Installation page explains how to go about this process.