
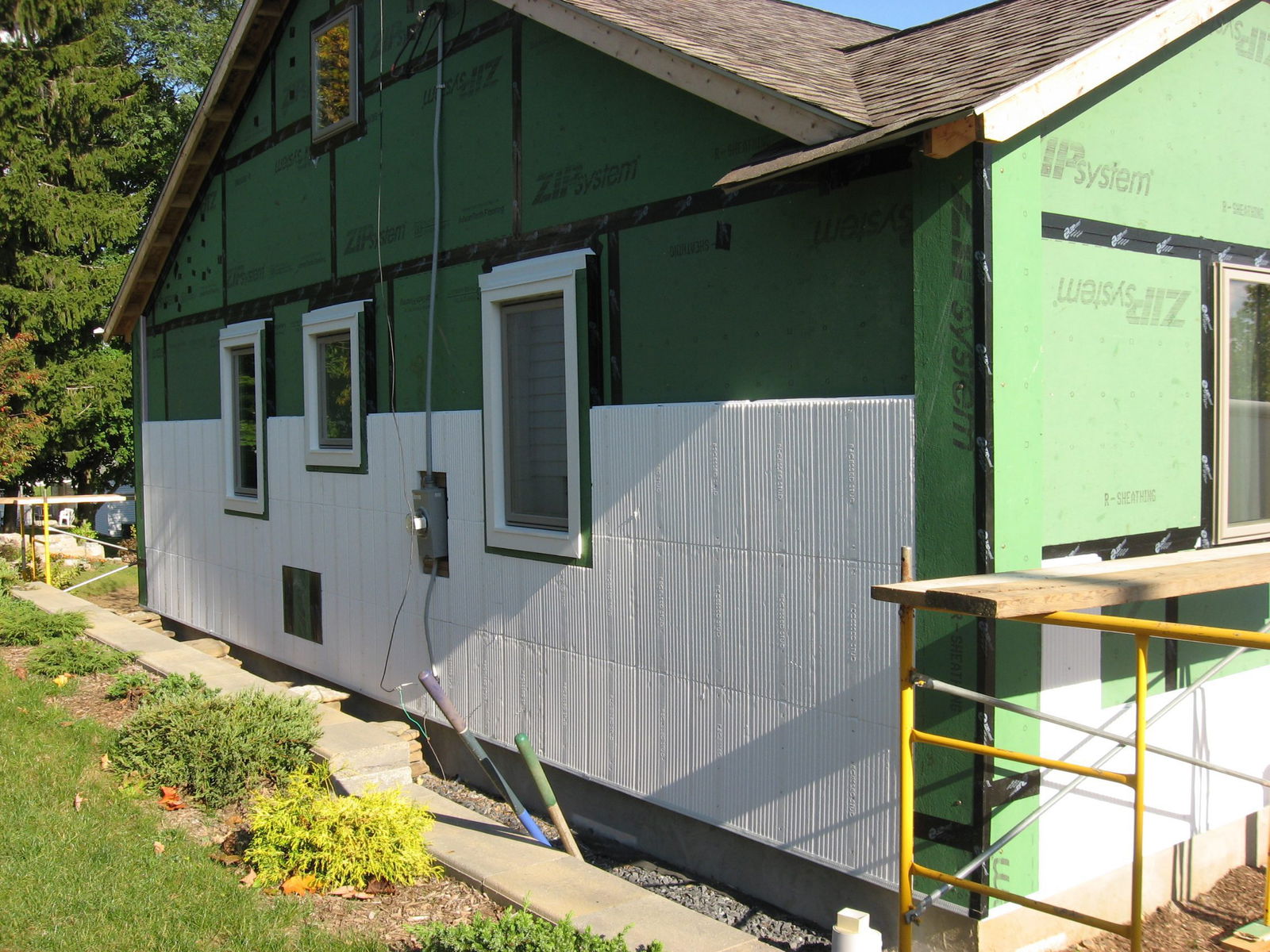
Exterior Continuous Insulation Project
Installation | Ordering Guide | Contact/Quote |
Back in 2014 we started working with a customer in Pennsylvania who had already been renovating his home for 3 years. Bill initially used InSoFast in his basement, but the next important step was the exterior. Motivated by his interest in building science, Bill planned his retrofit thinking, “build tight, ventilate right”.
The exterior retrofit project was extensive. Peeling off layers and layers of ineffective sheathing and decades old siding, the crew’s plan was to install Zip Sheathing, InSoFast EX 2.5 and Hardie Plank Siding. The house would look and feel almost brand new.
We spoke with Bill last week about his project. He gave us an insightful look into the process of renovating a home with smart, yet simple goals in mind.
What’s your professional background? What was your role for this project?
I went to design school and studied architecture and landscape architecture. I’ve worked as a carpenter for about 15 years. I was the designer for this project, but I consulted with engineers and specialists when I needed them. I can run the wiring, manage the drywall, finishing and the painting. I just repaired some flooring this week, so I wear a lot of hats.
But a job of this scale requires more bodies, so I had two different contractors and their crews come to work on the exterior. I oversaw the project, served as “quality control guy,” answered questions as they came up, and with the contractors’ help designed on-the-fly when necessary.
When we did the tear off two summers ago, I already had some experience with InSoFast, since I had used it in the basement of the house. I was already comfortable working with InSoFast and was able to answer questions from the crew during the exterior application.
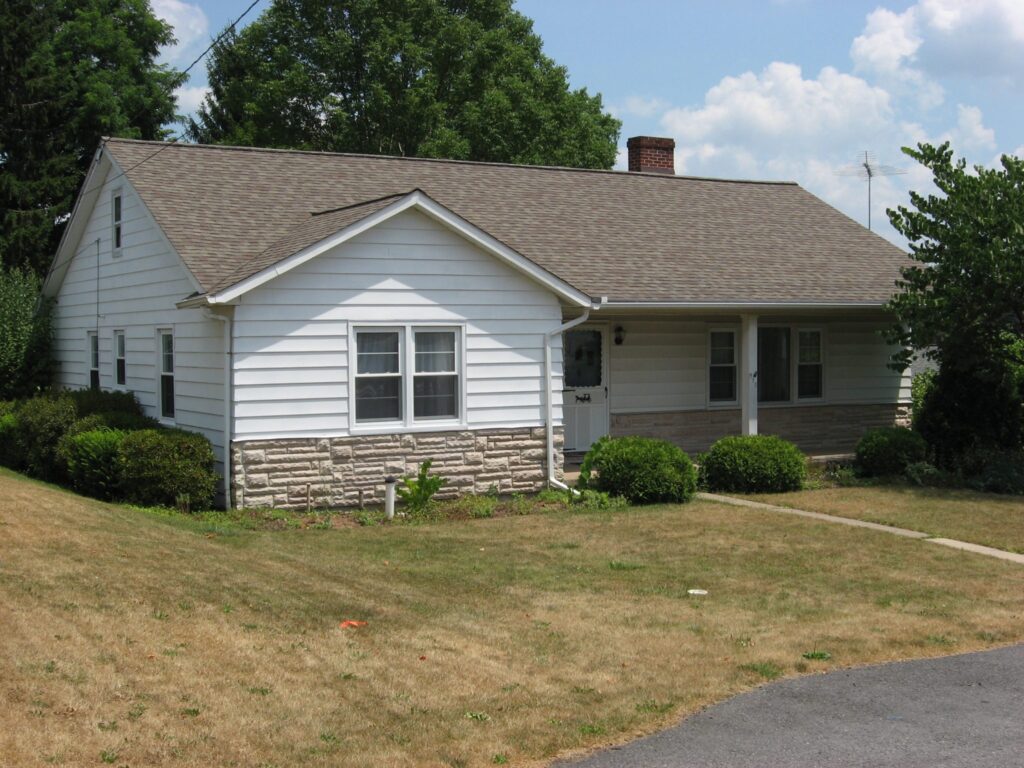
The house before the retrofit
Why did you choose InSoFast for the basement of the house?
The basement part of the remodel came first. I started studying building science around 7 years ago and got pretty deep into it. When we bought the house I wanted to immediately address problems I had seen in order of importance using my carpentry and remodeling skills.
We had to take care of water problems first. There wasn’t any standing water or visible water leaks, but we had lots of seepage. Our house is built on bedrock and a third of the basement is half-height crawl space. The dirt floor was exposed, so for the first 60 years of this house’s life, there was continuous seepage of moisture through the rock and into the house. Moisture was being drawn up through the house by stack effect.
I tried to address water first, then air, then vapor, then heat. When we considered vapor, InSoFast became the obvious choice for the basement. It was crucial in keeping the block walls warm, so condensation wouldn’t add to the moisture in the basement. If condensation ever forms or water penetrates the block walls, moisture will dry to the inside.
Let’s talk about the project in detail. What’s the story behind the house? Can you explain the retrofit process from start to finish?
The house has pretty much been torn up since day one. We closed on it in July of 2011 and before the end of July I was tearing out the basement remodel from the 1970’s. I had a 30 yard dumpster that was filled by early September.
In the summer of 2014 I hired the first crew to do the demolition, reframing of windows and door openings and installation of sheathing, windows and doors. We took off the aluminum siding from the 70’s and a layer of aluminized paper that was supposed to make some kind of thermal barrier. I can’t imagine that it worked very well. Behind that were cedar clapboards and homasote sheathing that were installed back in 1952. The house was stripped to the bones.
We reframed the window openings since all of the 19 windows and 3 doors were being replaced. Some were more recent double-paned vinyl windows while others were from 1952. The U-Values of windows are now much better than they used to be.
We used 4 x 8 sheets of Zip sheathing with ½ in of foam laminated to the back. Dean from InSoFast thought this step was overkill but my thinking was that it would provide a thermal break so that heat transmitted through the 2×4’s to the outside would be reduced. I also noticed that when installed, the Zip foam compressed against the framing forming a tighter air seal. There were a few awkward weeks in between crews during which we had a dark green-colored house with just the sheathing, building tape and the new windows.
Next the second crew installed the InSoFast, siding and trim. They had never worked with it before. I fabricated exterior jamb extensions and trim units to accommodate the 2 ½ inches of InSoFast depth and to receive the siding. We decided to glue and nail the InSoFast to the sheathing. The crew quickly ran a bead along the InSoFast stud and pressed the panels to the sheathing. Next they gun-nailed stainless steel ring-shanks through the InSoFast studs and completely through the sheathing. We used the same adhesive InSoFast recommends in basements between the InSoFast studs and the face of the sheathing. This seemed to be a pretty bomb-proof fastening method and we are confident it will hold up.
Did you run into any problems during the InSoFast installation?
The installation was a little tricky along the windows, corners and roof rakes where we wanted to use PVC trim (Versatex). Obviously, the PVC needed to be fastened to something. You can only screw or nail into InSoFast at the studs, which hardly ever ended at the corners, so we had to figure out a way to fasten the corners properly. Same with the windows and rakes.
On another note, the house isn’t perfectly plumb, level or square. One corner of our foundation is about 2 1/2 inches higher than the corner diagonally opposite. We ran a laser line around the house and began laying up the material from a chalked line. That meant that we had to do some creative adjusting when it came to the windows and the siding to get the lines to look how they should. But the crew was more concerned with those adjustments than they were with the InSoFast, which they didn’t have to think too much about.
You’ve said it’s important to “build tight, ventilate right.” Can you explain this mentality to our readers?
This is a common phrase used in the building science field. Building tight means ensuring that your house is as dry and airtight as possible. I learned very early on from Joseph Lstiburek (the principal at the Building Science Corporation) that you want to address water problems first, then air, then vapor and then heat. Insulating comes last in order of priority, but not always time. As I mentioned, in our basement, installing InSoFast addressed two problems, both vapor and heat.
Many of the problems I saw as a carpenter, particularly when remodeling houses built in the 70’s or 80’s were the result of inadequate water, air and vapor management. These houses typically had some kind of relatively impermeable vapor sheathing on the outside and then right behind the drywall was sheeted plastic. In between these two layers was the perfect place for moisture to get trapped. Sometimes these inadequacies would get completely out of control, leading to mold growth or severe damage to the structure.
Once the house is ‘built tight’ you have to ensure indoor air quality by “ventilating right”. When your house is drafty you don’t have to worry about this. All of the toxic gases that come out of your carpets and glues and finishes, along with odors from kitchens, bedrooms, and baths find their way to the outside. But once you ‘build tight’ all of that stuff gets locked in. Now that our house is ‘tight’ we have to ventilate mechanically. Old-timers will tell you that houses, ‘have to breathe’ but that doesn’t quite describe our situation today.
The project was completed over a year ago. Has there been a drastic difference in comfort since the retrofit?
This is the second winter with the InSoFast and the new siding. The first winter in the house was a real nail biter since I had ripped out the HVAC and there was no heating in the house at all. I bought oil-filled electric resistance heaters and placed them around the house. The house was drafty and the hardwood floors were way too cold to be comfortable with bare feet. Regardless, we could still heat the house before any improvements with just 35,000 BTU, which was a shock. Our original oil-forced air furnace was rated at 85,000 to 120,000 BTU.
My wife is very sensitive to blasts of hot and cold. Drafts are very unpleasant for her, so we chose radiant heat which builds up over time. Those first couple of winters my wife needed a blanket over her lap when we sat at the dining room table. She doesn’t need a blanket anymore and our daughter is usually barefoot, even in the winter. I can only imagine our energy bill is much lower than the previous owner’s bill.
As the house has gotten progressively tighter and better insulated we can now heat the house very easily. Right now it’s 10° outside with high winds and the wind chill is below zero. It was 68° when I woke and turned the heat up. Within an hour or so it was 72° and we’re holding that on 25,000 BTU. We’re not doing anything sophisticated or scientific, though there’s science behind the materials and techniques used in the remodel. The house is tighter and better insulated.
You’re now an experienced InSoFast-er! Do you have any advice or tips for our readers?
No basement wall is ever plumb or flat. The expanding foam adhesive is definitely the way to go for installing InSoFast in basements. In last month’s newsletter there was an article that featured a woman with uneven rubble stone foundation. The contractor suspended 2×4’s up against the InSoFast so that the expanding foam would push the InSoFast up against them. This process keeps the front line nice and plumb. This is the best way to go. I first saw this method on a This Old House Tom Silva feature. It’s a great technique, even on our block foundation.
The InSoFast insulation goes in very smoothly and quickly. A lot of people use screws to fasten for exterior projects, but glue and nails were very fast and secure. We used fiber cement siding which is extremely heavy stuff. There is no sign of the attachment giving out. The siding doesn’t even rattle. With aluminum siding you hear puckering and pattering but this stuff doesn’t make a sound.