
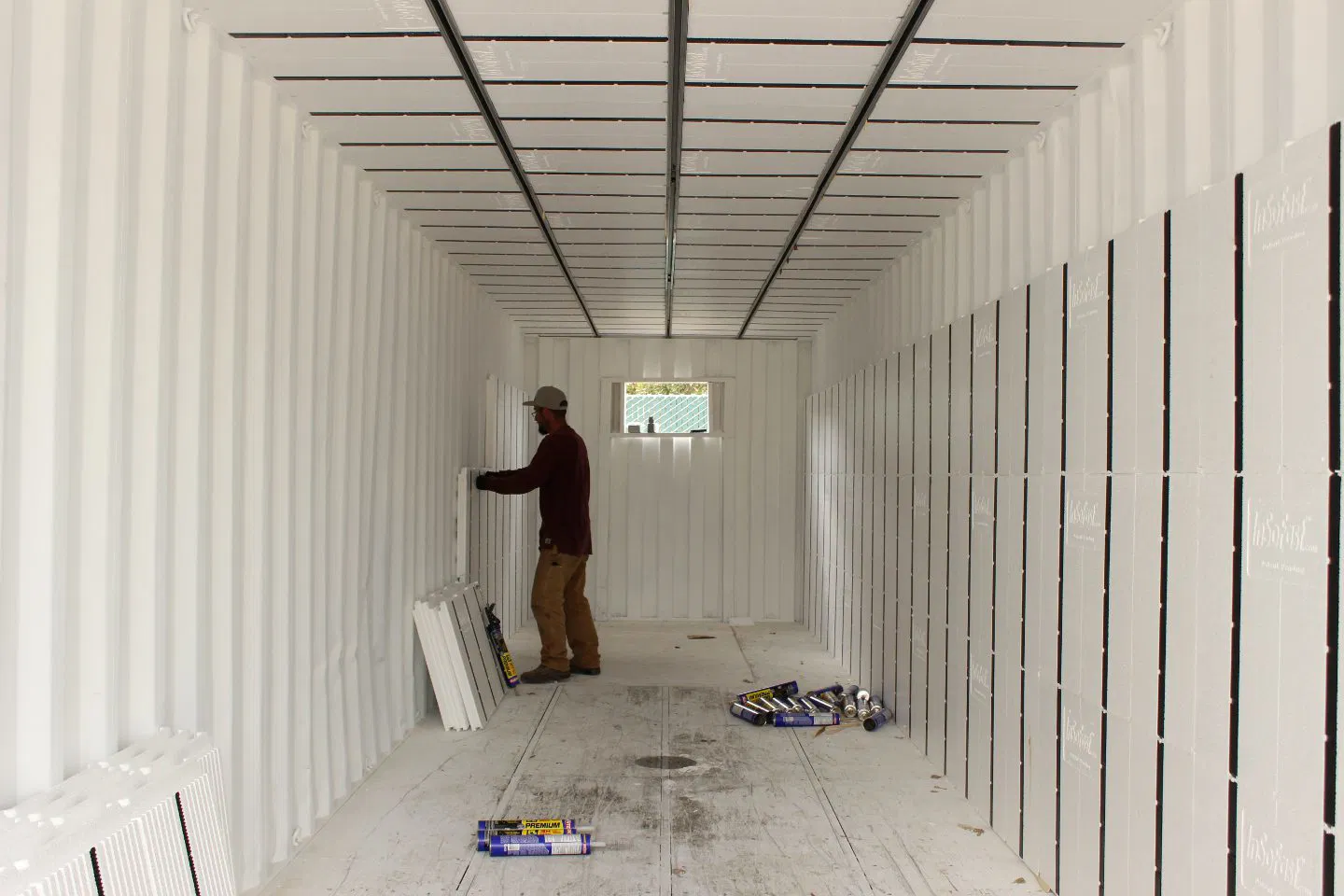
Southern Oregon’s Wine Country
Just outside of a small town in Southern Oregon’s wine country Shane has been diligently working on his farm, planning for next season’s crop. He’s using InSoFast to insulate several shipping containers that will serve as climate controlled coolers to dry his produce after harvest.
« How to » | « Order » | « Contact » |
Since Shane grows an edible product, the environment in the containers needs to be impeccably clean. Mold growth associated with insulations like spray foam and fiberglass, along with the off-gassing of blue board wasn’t going to cut it. Shane decided to try InSoFast in his first container citing the space-saving profile and ease of installation. Once finished, he quickly ordered enough InSoFast to insulate four more containers and plans to do even more in the coming years.
We had a chance to visit Shane onsite at Madrone Farms as the InSoFast panels were being installed in the second container.
Can you tell us about what you do?
It’s more about what I don’t do than what I actually do. My resume is a mile long. I’ve been working in engine repair and in the bicycle industry for approximately 30 years. Anything mechanical; heavy diesel stuff, boats, etc. Basically I’m the type of guy that can figure out a solution if you approach me with a problem. My father was a botanist and environmental scientist, so I was always around equipment and specialty electronics. We had a similar mindset. We tinkered.
Currently I’m in the cultivation industry in Southern Oregon. I’m working with some partners who have been friends of mine for quite awhile.
My technical term would be the Asset Manager, although there’s also a lot more involved with my job such as the implementation and design of the refrigerated containers.
How do the containers fit into the business?
The containers are essentially climate controlled rooms that will be filled with racks for herb drying. We will have humidity and temperature controls along with circulation so that the product can be dried, vacuum sealed and stored.
How did you come across InSoFast?
I did a whole lot of research into alternative insulation. I had talked with a few folks who were also designing containers for their own companies. We immediately decided to avoid spray on or batted insulation because of the mold problems that typically tend to develop with such material.
I have heard of so many farmers who have used spray foam and had bad results down the line. Every older container I’ve seen is loaded with black mold everywhere. It’s nasty. Plus, you lose a lot of space with those kinds of installations. As I read more about products like blue board I started to learn about off-gassing, which I also wanted to avoid.
I think I came across InSoFast on a YouTube video. I followed up with some phone calls. The reality is that with the space savings, the R-Value being pretty high and the ease of the installation; it just made sense to us.
We decided to do a test run with one container and now we are building out four.
Can you explain how exactly you’ve gone about installing the InSoFast in this container?
You could call our installation method “on-the-fly-learning.”
We’re currently working on the roof of this container in a different fashion than we tried out in the first container. We’ve determined that temperature is a key factor with installing the panels, particularly on the roof. In metal containers, the cooler the better. I’d suggest doing this project in the winter instead of during a hot Oregon summer.
Particularly in some of the container roofs you’ll find a lot of dents, which is why I came up with a new way to keep the panels up there. It wasn’t flat enough where I could just let the glue set a little bit and push the panel in place. There were times when I could get the panels to stick and the easiest way to keep it up was with a 2×4 support similar to a drywall jack. In the first container, I decided to add furring strips over the panels that attached directly to the ceiling of the container. In the second, we have pre-installed a track that will hang our racks. The panels are fit between.
Side Note: InSoFast recommended against screwing through the walls of the container and attaching metal tracks between the panels. This disruption to the insulating layer can act as a thermal bridge and condensation point. Shane has assured us that he will be sealing all connections and insulating the roof to help minimize eliminate the bridge.
Down the line, we’re talking about growing living roofs on the top of the containers to keep them cooler. We will stack them close together and put a big ol’ gravel living roof succulent plant system up there.
The floor will be left alone for the season because I can’t get it done in time. Next season I’d like to add some trim on the wall for some more stability, put in a cove base and some vinyl. Really I just need something that is completely inert and moppable. It doesn’t need to look nice; it just needs to work.
Have there been any quirks in the installation process?
Essentially, we’ve been fighting a few factors with the containers.
The biggest struggle with this whole process has been the condition of the surface behind the panels. The challenge is that these are one trip containers but C-grade. We were experimenting with the price, so C-grade means the container fell over.
The reality is that these walls look really smooth and nice with InSoFast but behind the panels are many dents. They’ve been dented, damaged and manipulated by other means. They are not perfectly true like a concrete or interior wall would be. Since we are working with something that isn’t as flexible as a spray-on application, placing it over the top of these imperfections can be tricky. But we’re finding that it works just as well. You just need to use enough glue, mark the void spots and fill.
We’re also fighting the condition of the surface behind the container. Our product has to be surrounded by food grade materials at all times. It is a consumable product and it’s on the open marketplace, all organic. We used extremely low, almost No-VOC paint to seal up the container from any contaminants. Now we are installing the insulation directly on top with the glue.
You chose to install the panels horizontally. Can you talk about why the structural properties aren’t as important to you?
We’re not mounting anything to the walls like kitchen cabinets, etc. We’re essentially creating a large cooler. When we first started installing the panels we just placed them that way because it seemed to work regardless. I’m not sure if one way works better than the other, but I sure can’t rip them down.
Side Note: For shipping containers, InSoFast recommends running the studs horizontally even though they are actually designed to run vertically. This allows the studs to get the most contact possible on the corrugated surface of the container. The vertical installation is sufficient for Shane’s containers because no heavy objects will be hung directly from the studs.
One of the main properties of our panels is that the built in studs provide structure.
Why go for InSoFast if you don’t need the studs?
The other panels that I researched were more expensive and off-gassing was present. But since we aren’t mounting anything to the walls, the stud feature wasn’t what sold us. We just needed an affordable, safe, climate-controlled space to grow our crop.
I designed my own rail hanging system that comes off the ceiling to dry the product. We will use a drying basket with a 36 in diameter which will utilize two of the rails on the ceiling. As long as this is structural enough, we are good to go.
In terms of labor, you’re hiring someone who already works for you to do the job. You’re not hiring outside contractors?
Correct. I didn’t need to hire outside which is the beauty and ease of this application. My worker can hold the panel himself. He can glue the panel himself. And he can get the box off the truck himself.
More people on deck obviously make it go faster but it’s not necessary. When you’re talking about other building materials – for instance, a 4×8 sheet of plywood or a larger sheet of anything it’s a little tricker for sure.
Would you mind telling us the average cost to complete each container?
I’d have to pencil out the exact costs, but as a vague estimate: the container is $2,000, InSoFast is around $2,000, with $1,000 for the HVAC. Then there’s the piping, electric, labor and what-not.
InSoFast provides free shipping direct to a project site. Was this important to you?
As far as shipping goes, all I have are Lowe’s and Home Depot in terms of resources for these parts. Medford is a town of 50,000 and Grants Pass is 35,000. These aren’t huge communities and I don’t have every option. We’re out here in the middle of 30 miles from anywhere in Southern Oregon.
So the boxing system made it really easy for us as well. It made it easy to load, easy to deal with, it made it easier for us to get essentially. If you’re going to ship a whole 4×8 sheet of palleted material it’s a little harder to acquire, let’s put it that way. I’ve been procuring things from here to Alaska. Procurement is huge. If you can get your hands on it and it comes to you, that’s what you want.
Even if the estimate for blue-board had come in as less, which it didn’t, I still would have chosen InSoFast because of its installation capabilities. The reality is that it sure is easy. I only need one guy carrying it around and installing it. That’s big.
Do you have any ideas for helping others in the industry in terms of the containers and refrigeration?
Out here in the middle of nowhere the containers serve a really unique void in terms of the fact that they are inexpensive in comparison to building things like barns. They are also mobile, so they could be disconnected from the grid and loaded on a truck.
What I’d like to do in the future is actually create custom containers for folks on a semi-commercial scale. There are a couple people who are doing a cookie-cutter kind of product but I’ve found that the container, the way it’s insulated and the set-up is completely different for everyone. One container doesn’t necessarily fit the mold for each unique site.
I do have a wife and kids though, so I don’t want to work all of the time.
Thanks for showing us around Shane.
For more on this project, follow us on Facebook. We’ve been posting video interviews with Shane from inside the container.